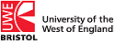 |
Conservation of Cast & Wrought Iron |
 |
|
3 Shaping iron
Cast iron
Pig iron (ingots cast from the blast furnace, see Section 1.0) form the raw
material for foundries to recast into architectural and structural components.
The process as developed in the middle ages is still widely used today with some
modifications. Originally developed by John Wilkinson around 1794, a coke-fired
cupola furnace was used to melt the iron, modern equivalents now being fuelled
by gas, oil, or electricity. Molten metal is run into a crucible or ladle and
poured into a sand mould to fill a void shaped like the final component. After
solidifying, the casting is broken out and the runners/risers which fed in the
metal are cut off. A ragged edge (flashing) often caused by seepage of metal
between the two halves of the mould is dressed off, (fettling) and the raw
casting is blast-cleaned to remove sand deposits. |
 |
Moulds - Traditionally greensand was used for moulds, set in open metal boxes as
illustrated. Greensand is a naturally occurring clay/sand mixture used slightly
damp, capable of giving excellent surface definition. Whilst this process is
still used for small quantity production, nowadays the more mechanised foundries
use resin-bonded sand cured by chemical hardeners or gases to give more
consistent and accurate castings.
Patterns - A pattern to form the void in the mould is made slightly oversize to allow
for shrinkage of the metal, (about 1% for iron). Patterns are usually made of
wood, but 2-pack resins and aluminium are often used in high-volume
applications, and patterns for one-offs can be shaped easily in wax, expanded
polystyrene, or plaster. An original component can be used provided that:
Surface detail is sufficiently crisp. New castings 1% shorter than originals
will be acceptable. (or the original can be built-up) The shape of the original
will allow it to be drawn from the mould.
Shapes that will not draw from the mould, and hollow castings, require loose
mould-pieces called cores. These are shaped blocks of sand cast in a
specially-made box, hardened to become self-supporting, and placed inside the
mould to form internal shapes.
|
Wrought iron
 |
Wrought Iron is highly malleable, ductile and forge-welds readily, properties
exploited by the blacksmith to create the many delicate and ornamental designs
of traditional wrought ironwork such as scrolls, leaves, masks, etc.
Processes included punching, upsetting, drawing-down, fullering, swaging,
twisting, cutting, etc. Joints were generally not secured by bolts, but by use
of mortices & tenons, collars, wedges, pins and rivets, or by forge welding.
This entails swelling up the ends to be joined, heating them to white heat,
beating them together to fuse, and finally truing up, forming a weld
approximately 80% as strong as the original section. Simple leaves were formed by hammering thin sheet down onto a metal stake.
More complex shapes such as large leaves, shields & masks were formed by doming
out from the reverse filling with lead and cutting in detail from the front
using fine chisels and punches. (repousse work) The smith would make many of the
tools himself, often developing tooling especially for the job in hand.
In refurbishment work it is important to use the correct traditional
materials and techniques, not modern equivalents, if subtle detailing and
historic integrity is to be preserved.
|
|
|