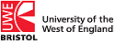 |
Conservation of Cast & Wrought Iron |
 |
|
4 Surveys
The need for a survey - Metal structures are often prominent, complex, and
highly-loaded. Conservation work on iron can be intrusive, non-reversible and
costly. It is therefore important metalwork is surveyed expertly before
conservation work starts so as to:
- determine the method and materials of
construction
- establish fully the nature and extent of defects/deterioration
- facilitate strength assessment
- allow the least intrusive and costly
conservation options to be planned.
|
Preparations - Old coatings can be useful indicators of past movement/corrosion
in joints, impacts, and water leaks/ponding, so their general removal should be
unnecessary, unless exceptionally thick. It may be necessary to lift or
partially remove flashings, claddings, panelling, or floorboards temporarily,
but extensive dismantling of metalwork should be avoided. A range of equipment
is available for viewing internal spaces, such as endoscopes and CCTV, which
require access holes of only 12mm or less. |
Paint sampling - Almost all historic metalwork was painted from new, and
evidence of past priming, under and finish coats often survives. These should be
sampled as part of the survey, and an attempt made to identify earlier finish colour(s). If paintwork has failed generally or little survives, remnants can
often be found intact in crevices and protected areas. A full-depth sample from
each area of the structure should be dislodged by scalpel or chisel, and
inspected on edge under a X20-X40 microscope. Layers of paint and dirt should be
sketched to scale, and photo-micrographed. Samples should be retained and
archived. Colours should NOT be matched to those seen in samples as binders
usually darken on drying, and some colours change dramatically with age.
Pigments should be laboratory-analysed and their formulation used to mix new
paint using traditional materials. |
Condition - Evidence should be sought for general and localised defects
including:
Overloading |
Distortion, rust or frost heave, fractures |
Settlement, movement |
A survey of levels may assist, but original misalignments
may exist |
Mechanical shock |
eg, vehicle impacts |
Thermal shock |
Fire, quenching, past weld repairs |
Original material/manufacturing defects |
Voids, inclusions, delamination, cracks |
Badly executed alterations and repairs |
|
Corrosion |
Especially in joints, areas of poor drainage or ventilation,
splash zones, and around dissimilar metals |
|
Non-Destructive Techniques (NDT) for inspecting metals on site
- to expose
small or internal defects on highly stressed parts. Surfaces must be
blast-cleaned first.
- Dye-penetrants - A low-viscosity coloured liquid is sprayed onto the surface
and allowed to enter cracks by capillary action. The excess is removed and a
white ‘developer’ powder applied generally. This draws out any penetrant within
cracks, revealing their position.
- Magnetic-particle penetrant - Similar to above, but the penetrant is a
magnetic-particle ink drawn out of the crack by application of a hand-held
magnet.
- Ultrasonic probe - Reflected beam of ultrasound indicates presence of internal
flaws.
|
Survey Report - The survey report should be detailed, and ideally should
include:
- Description of the structure, identifying its materials.
- Causes,
nature, extent and location of defects/deterioration.
- Record of active
deterioration, and estimate of its rate of progression.
- Structural analysis.
- Paint sample analysis.
- Schedule of recommended repairs.
- Specification for
conservation works.
|
|
|